Combined EGR and Bilge Water Treatment System - CD-EGR
Improving by removing: Cleaning both bilge and EGR bleed-off water with the effective flocculation technology.A unique combination
Marinfloc’s CD EGR unit is the first ever, class approved, system for treating water from two different annexes. The solution offers a two-in-one streamlined approach to minimize equipment, installation, operational cost and CO2 footprint. While bilge water and EGR bleed-off water fall under different MARPOL Annexes, necessitating segregation, our system ensures they remain separate. This includes distinct holding tanks and sludge tanks. System segregation valves prevent any mixing, including the sludge generated during treatment. The class-approved automated switch-over sequence, managed by system automation, ensures seamless operation. From the control panel, operators can effortlessly choose the waste stream for treatment. The Whitebox® oversees, records, and segregates the vital discharge parameters, ensuring accurate record-keeping as mandated.
A single high-end separator for two waste streams eliminates budgetary compromises for new projects.
Utilizes flocculation technology, eliminating the need for cartridge filters and centrifuges.
Eliminate the need for a separate bilge water separator, reducing capital expenditures.
Lowest CO2PEX due to low energy usage
Operational Savings: Less classification costs, spares, service and consumables
A single high-end separator for two waste streams eliminates budgetary compromises for new projects.
Utilizes flocculation technology, eliminating the need for cartridge filters and centrifuges.
Eliminate the need for a separate bilge water separator, reducing capital expenditures.
Lowest CO2PEX due to low energy usage
Operational Savings: Less classification costs, spares, service and consumables
Unwavering support. Top-notch training.
Safer waste streams and better workflow. At Marinfloc, we are dedicated to helping you manage and minimize the maintenance of your onboard wastewater systems.
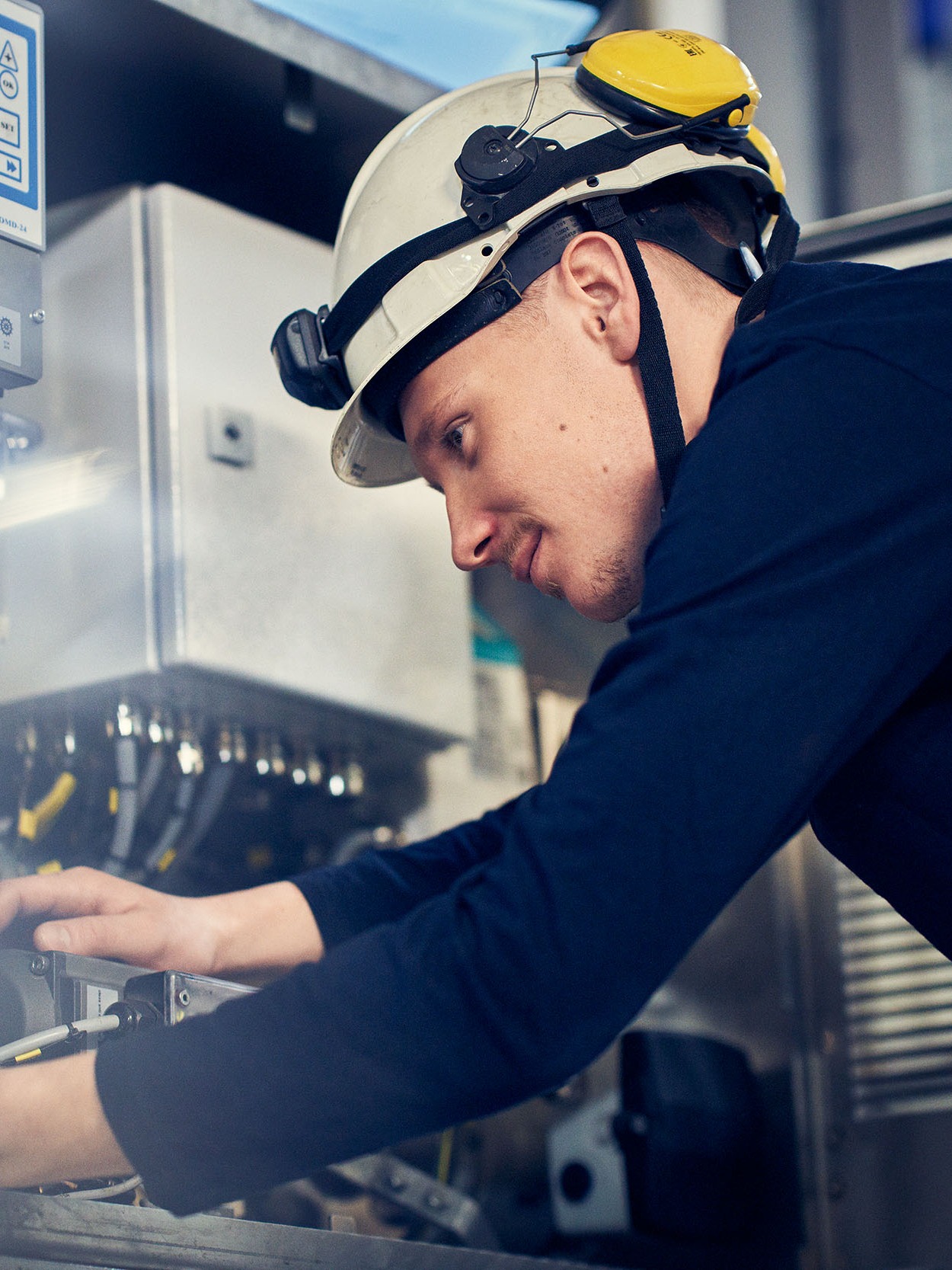
Operating principle
The Marinfloc combined system efficiently manages both bilge water from bilge wells and EGR bleed-off water from engines. It features a unified separator for water treatment and a recorder or a WhiteBox® to monitor overboard discharges. The bilge water component includes a bilge holding tank and an oily bilge (sludge) tank. The EGR component is equipped with tanks for bleed-off water and sludge, with an optional buffer tank to regulate water volume, which overflows to the EGR drain tank as needed.
Three-way valves facilitate the flow of water and sludge between tanks and the separator, ensuring proper treatment. These valves include:
A suction valve to choose the water source between the EGR drain tank and the bilge holding tank.
A recirculation valve to direct treated water back for further processing if necessary.
A sludge valve to manage the direction of sludge to the appropriate tank.
The system operates in two modes: EGR bleed-off water discharge and bilge water discharge, defaulting to EGR mode under specific conditions like a power drop, to ensure continuous, compliant operation.
The cleaning process of the system includes:
Oil Separation: The system separates free oil from water through gravitational methods in the oil descaler. Accumulated oil is then transferred to the vessel’s sludge tank once detected by an oil sensor.
Aeration: Compressed air is introduced into the circulating tank, mixing with the water to dissolve air maximally. This process helps in the continuous discharge of bilge water, maintaining the system's operation.
Flocculation and Forced Flotation (DAF): In this stage, water is directed to the flocculation tank where chemical dosages are precisely controlled for optimal flocculation. A layered separation occurs, with a foam layer being continuously removed to the sludge tank.
Filtration: The filtered water, now clearer but possibly slightly discolored, passes through a series of filters to reach an effluent quality of <15 ppm. This comprehensive filtering stage ensures the removal of any remaining contaminants, including oil and flocks.
Additionally, an Oil Content Meter (OCM) is incorporated to ensure compliance with environmental regulations by monitoring the oil content in the water, which is typically set to not exceed 15 or 5 ppm.
Flocculation is a water treatment process in which solids come together to form larger clusters, or flocs, which are then removed from the water. This process can occur naturally or with the assistance of chemical agents. It is a common method of wastewater treatment and drinking water purification.
DAF is a water treatment technique that removes suspended particles like oil or sediments from liquids. By dissolving air under pressure and releasing it at atmospheric pressure in a flotation tank, tiny air bubbles attach to the particles, making them float to the surface for removal.
No other waste stream on a ship is so closely connected to million-dollar fines and imprisonment as bilge water. Bilge water contains various pollutants from the engine room, not just oil and water. Marinfloc has the expertise, technology, and flexibility to provide tailored solutions for your needs.